How Telematics Is Transforming Underground Utility Operations
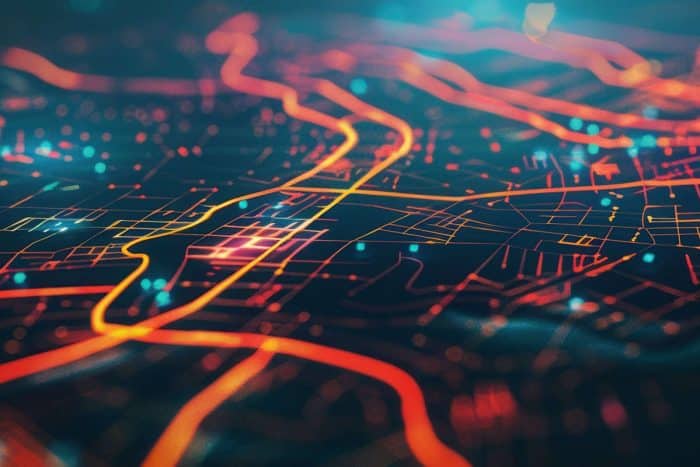
By Oscar Collins
Businesses that engage in logistic operations, like utilities, can immensely benefit from telematics. This technology combines GPS, monitoring sensors and onboard diagnostics to improve fleet performances in more than one way.
Learn how it impacts underground utility operations, as well as integration methods and adoption challenges.
The Benefits of Telematics Integration
Here are a few ways this vehicle-tracking technology helps utility professionals.
1. Higher Efficiency
Regardless of industry, data has always been critical to operational productivity. Telematics systems pool an impressive amount of raw information that can be leveraged to create insights to boost productivity and make informed decisions.
For instance, in the utility field, location data means no more phone calls when service technicians need to find a vehicle that broke down mid-drive. They can conveniently enter the truck unit number on a mobile device and find the directions to get there via GPS.
Without telematics, the typical response for this scenario would be to call the crew, which is potentially time-consuming. Furthermore, such a method is less efficient, especially if the team you’re trying to track is in an area with poor reception or is out of reach.
2. Enhanced Safety
Telematics protects company assets and utility workers while on the road by providing real time notifications on driving conditions and behaviors. This advantage allows contractors to remotely track speed, fuel use, idle time, and other crucial data, giving them live updates on all sorts of ground situations.
Installing an AI-equipped black box with outstanding tracking capabilities also enables leaders to respond more promptly to emergencies or compromising events. In a service-based industry, faster mobilization can help keep loss to a minimum.
Additionally, telematics monitor driving habits and send feedback to the headquarters. Distracted driving is a prevalent occurrence that has led to thousands of vehicle crashes.
In 2022, 3,308 people died because drivers diverted their attention from handling the wheel. Data on driving habits is essential for managers to be informed of reckless driving instances and file an appropriate sanction for the driver’s lack of personal responsibility. Alternatively, telematics encourage better habits behind the wheel and promote safety.
3. Significant Operational Savings
Telematics promotes cost efficiency by optimizing service routes and enhancing navigation systems to prevent unnecessary logistic detours. With accurate tracking, utility employees can determine shortcuts or trafficless roads to their destinations, potentially saving 60% to 70% in fuel consumption costs.
The switch from preventive to predictive maintenance also lets companies lower maintenance-related expenses. Trucks could break down earlier than their scheduled maintenance, leading to a costly fix.
Rather than relying on the timetable, telematics devices analyze actual real-time data and use regular diagnostics updates to predict the best time for servicing. As a result, you save money and extend the life of your equipment and vehicle.
4. Sustainable
Utility providers promote sustainability by decreasing their travel miles. The industry is criticized for its high emissions because it’s dependent on fossil fuels for energy generation. Installing in-car technology in utility service trucks will help minimize their operations’ carbon footprint.
It’s one of the best workarounds for those who want to showcase their commitment to sustainability and planet protection.
3 Methods of Successful Integration
Here are three ways to effectively incorporate telematics in underground utility operations.
1. Collaborate with a Provider
Utility professionals must look for telematics solutions that are customizable and scalable. These two features are essential. Every fleet has different needs, challenges and requirements. Tracking areas of optimization and performance can vary between assets.
Therefore, it’s crucial that a tool can be modified to meet the needs of each truck or piece of equipment. Meanwhile, scalability is integral when managers want to prioritize a particular area to improve.
2. Provide Comprehensive User Training
For some people, telematics could be a completely new experience — adequate training is essential for a smoother transition. Staff must fully understand the system’s capabilities and features. This knowledge will help them optimize vehicle tracking to its full potential. Without appropriate education, the tool won’t serve its purpose.
3. Understand Data to Support Decision-Making
Data is the foundation and power of telematics. Utility professionals must learn to analyze and extract insights from raw information and use them to make informed decisions. For example, managers can use driver behavior data to determine who among their drivers requires retraining on road regulations.
Challenges with Telematics
Companies must be aware of the technology’s drawbacks. Learning about them can help utility professionals adjust their integration wherever and whenever necessary.
One is the need for more actionable data. Data input is telematics’ greatest strength. However, it’s also a weakness, creating overload and confusion among users.
Customers need simplified and directly usable information to guide immediate and strategic decisions. However, telematics includes way more unnecessary details. An option to filter what users deem important can make the tool more effective and user-friendly.
Another challenge is the available connectivity on the site. Since it requires the internet, connectivity infrastructure like Wi-Fi or cellular sources must be present at the job location for users to link to data sources. Utility staff will have access to their phones on-site to access information, which may negatively impact their driving habits or work performance.
Underground Utility Operations Benefit from Telematics
Telematics adoption is expanding. Utility professionals can now solve significant operational concerns with this tool. The key to optimizing its use is adequate training for the staff to understand how to interpret data and use the insights in guiding their decisions.
Oscar Collins is the editor-in-chief at Modded. He’s written for sites like Contractor and StartupNation. Follow him on Twitter at @TModded for frequent updates on his work.