8 Areas of Inefficiency to Address in Your Underground Utility Operation in 2025
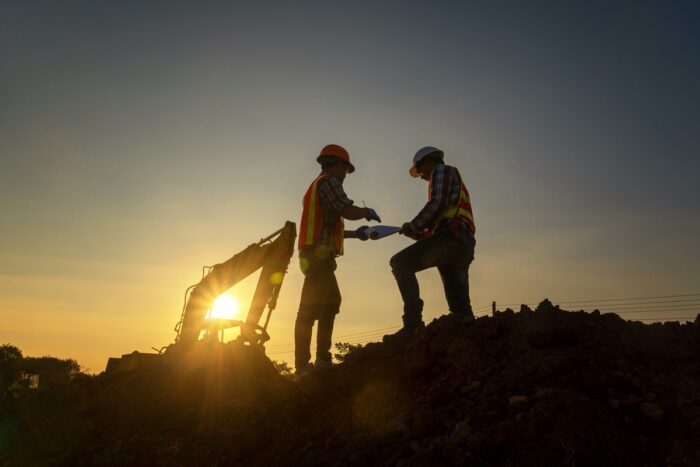
reduces delays and enhances safety.
By Oscar Collins
Underground utility contractors face an array of inefficiencies that delay projects, increase costs and even pose safety risks. From logistical challenges to innovation resistance, a lack of optimized functionality impacts productivity and profitability.
However, with strategic planning, proper training and the right technology, contractors can mitigate these issues. Here we examine the most common areas of inefficiency and actionable solutions.
1. Poor Planning and Its Ripple Effect
One of the most significant inefficiencies stems from poor planning. When projects lack a clear roadmap, contractors face unexpected delays, material shortages and mismanaged timelines.
Solutions include:
- Project management software: Use planning programs to plan each phase, assign tasks and track progress. Correct planning reduces wastage and optimizes resources.
- Pre-job assessments: Conduct thorough pre-work assessments to identify and anticipate potential obstacles. Never exceed the vehicle towing capacity by overloading vehicles to cut corners — doing so can cause avoidable mechanical failure and accidents. Trucks should have the capacity to haul equipment to all parts of the site instead of relying on lightweight but inefficient machines.
- Material deliveries: Careful and strategic delivery scheduling avoids storage and labor challenges.
2. Procurement Delays and Material Management
Projects can halt due to material shortage. However, stockpiling materials increases storage expenses and site congestion.
Solutions include:
- Adopt just-in-time delivery inventory management: Ensure materials arrive when necessary. AI-driven programs anticipate material requirements according to various project stages.
- Network reliable suppliers: Blockchain technology improves transparency in supply chain management, ensuring supply availability.
- Prefabricate: Utility projects for gas lines, electrical and fiber connections, and water pipes can use prefabrication to speed up distinct project phases and minimize time worked in cramped utility tunnels. Use off-site fabrication for increased quality control when making junction boxes, pipe sections and vaults.
3. Inadequate Use of Technology
Many contractors still rely on outdated methods for surveying, mapping and tracking utility lines, leading to errors and inefficient resource use.
Solutions include:
- Use the 811 system efficiently and log a ticket for utility identification for timed responses and avoid project delays. Incentives may encourage crews to follow new protocols, and efficiency bonuses are a great way to ensure compliance.
- Invest in mapping services that use ground-penetrating radar or GPS mapping to avoid costly underground utilities strikes and project delays.
- Survey large sites with drone technology.
4. Lack of Communication and Coordination
Miscommunication between teams, suppliers, and project managers can lead to costly mistakes and reworking. Likewise, inefficient communication and uncoordinated work can trigger cascade events that can claim lives, such as trench cave-ins.
Solutions include:
- Project management platforms: Collaborative management programs ensure all teams have the relevant information to their work. Invest in proven solutions like Procore or Autodesk Construction Cloud.
- Daily check-ins: While meetings may seem redundant, they are vital to keeping all teams aligned and informed.
- Reporting protocols: Ensure the labor force knows the protocols for reporting delays, safety concerns and material shortages to save time and facilitate swift remedial action where necessary.
5. Damage Prevention — Locating Utilities
One of the biggest inefficiencies lies in not identifying the location of existing utilities before repairs or additions. Line strikes can cause a negative cascade that may result in severe danger and fatalities. Such events resulted in 64 deaths in 2022.
Solutions:
- Call 811: The “call before you dig” initiative ensures consultation with the correct utility companies to provide the location of any power, gas, electrical and fiber lines in the vicinity of the project site.
- Do potholing before excavations: Utility potholing or daylighting ensures the identification of any existing underground utilities before heavy equipment like excavators are used for trenching. Training and education could help reduce the risk of line strikes.
- Follow best underground utility digging safety practices: Correctly trained workers remain alert to utility markers, which ensures they follow correct procedures to confirm the exact location of utility lines. With potholing and proper clearance, safe trenching is possible. Increase worker training and skills refreshment with courses in trenchless digging and mentorship.
6. Geological Changes and Risk Increase
Rain, land movements and soil quality affect the results of compaction and trenching, which can create hazardous working environments and danger to staff and equipment. A high rainfall season can raise the groundwater table, which may cause sinkholes to form that can topple heavy machinery.
Solutions include:
- Conducting thorough site surveys before breaking ground for utility laying ensures the inclusion of risk reduction and mitigation costs in quoting.
- Real-time soil monitoring sensors — early detection of changes prompt appropriate responses and risk management.
- Techniques such as soil stabilization can help prevent landslides and other earth movement due to water and geological events.
7. Preventing Vehicle and Equipment Damage
Improper transportation of spare parts, materials and labor can cause vehicle damage, as can incorrect waste management and movement. Using designated trucks for specific waste increases efficiency for site clearance.
Solutions include:
- Use trailers with the correct axle load capacity to prevent strain on vehicles and decrease risks associated with breakdowns.
- Follow weight distribution guidelines and axle capacities when transporting heavy loads, especially across uneven ground or compromised terrain.
- Don’t cut costs. It may be tempting to opt for a trailer with a carrying capacity of 3,500 to 10,000 pounds if your materials are just below the 10,000-lb mark. However, if you’re hauling a lot of large equipment, it might be best to spend more on a specialized trailer with a larger carrying capacity. Just make sure to tow with a heavy-duty truck equipped to work with that kind of trailer.
- Conduct regular vehicle maintenance checks to avoid breakdowns.
8. Safety Issues With Backfilling and Compaction
Underground utility management — whether laying, repairing or maintaining — often requires large scale trenching. Closing sites requires backfilling and compaction to ensure even pressure on lines. However, incorrect backfill or compaction can lead to dangerous situations like vehicle rollover, ground instability and long term structural issues. This is especially concerning when utilities run under roads or other infrastructure.
Solutions:
- Controlled backfilling techniques: Layering — mixed with recycled aggregates — can increase stiffness by 1.6 times, ensuring adequate density and trench strength.
- Soil compaction tests: Always conduct compaction tests before moving to the next layer or final concrete slabs to avoid sinkhole formation and stability issues.
- Effective operator training: Ensure operators are skilled at correct compaction techniques when using equipment like vibrator compactors.
Efficient Utility Construction
Addressing inefficiencies for underground utility contractors improves productivity, reduces delays and enhances safety. Modern technology, refined planning strategies and better communication are critical when streamlining operations. Proactivity ensures contractors operate efficiently for long-term sustainability.
Oscar Collins is the editor-in-chief at Modded. He’s written for sites like Contractor and StartupNation. Follow him on Twitter at @TModded for frequent updates on his work.