One Size Doesn’t Fit All
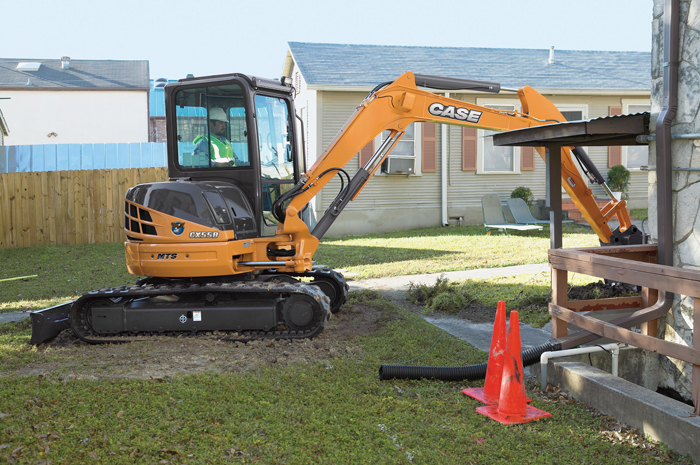
No matter what the application, compact excavator operators have to have the right foot forward — or the right track. A common misconception is that one track fits all applications, when in fact there is a perfect track for each need on the jobsite. Selecting the correct style can be the difference between optimal operation and unnecessary downtime.
Getting Down to Business
There are advantages to both steel and rubber tracks depending on the operating environment. Rubber tracks are a good option when working in soft conditions because they limit the amount of damage to finished surfaces.
If rubber tracks are used, it’s important to avoid harsh environments such as jagged rocks, demolition rubble and more, which could shorten track life. Operators should make it a priority to stick to relatively flat services.
Steel tracks are used due to their grip and traction. When choosing a steel track, there are a number of things to take into consideration in order to achieve the highest level of flotation and performance. Track width and the total number of grousers are two of the most important elements.
Some compact excavators also offer hydraulically retractable tracks that allow operators to move through narrow openings. After passing through a tight space, they can expand to stabilize the machine and give it greater digging power.
Proper Operation Makes a Difference
The undercarriage of any piece of equipment represents a significant portion of the equipment’s purchase price. Proper operation is critical when it comes to controlling the cost of these wear items and ensuring the longevity of your fleet.
For starters, operators should first check the ground conditions to determine whether steel or rubber tracks should be used depending on the need to control ground pressure or navigate debris. Travel equals wear, so finding out how to minimize the amount of travel the machine makes on the jobsite is crucial.
When it comes time to start work, operators should try to make wider turns, such as Y-turns. Counter-rotation, or pivot turns, cause accelerated wear on the machine and increases the potential for de-tracking of rubber-tracked machines. Operators should also try to avoid continuous turning on the same side, which can cause asymmetrical wear.
Constant operation on a slope or hill in one direction can accelerate wear by placing greater force on one side. Operators should travel straight up or down the slope, with turns being performed on level ground. Some jobs require hillside work, but minimizing time on the slope will payoff in reduced wear and load to the undercarriage.
It’s also important for operators to control track spinning, which can increase wear and decrease productivity, by decreasing the blade or bucket load. Higher speeds and excessive travel in reverse can also cause premature wear, so operators should monitor their speeds closely and avoid unnecessary travel in reverse.
Maintenance Means More
Proper care of a machine’s tracks can significantly minimize maintenance costs, increase uptime and impact the longevity of the compact excavator.
Owners and operators should monitor track tension and adjust it according to jobsite conditions. If the tracks are too loose or too tight, it could lead to excessive wear, instability, breakage or even derailment. Proper tension of steel or rubber tracks also ensures the machine puts its available power to best use.
Also, it’s important to keep the undercarriage clean. At the end of the day, operators should clean out the mud and debris from the undercarriage. Special attention should be paid to the cleanup of rubber tracks since buildup can cause them to stretch.
Another essential operator requirement is regular inspections of the undercarriage for any signs of excessive or uneven wear, as well as damaged or missing components. It’s also required to adhere to manufacturers’ recommendations and routine maintenance guidelines.
Lastly, ongoing operator training is beneficial in track longevity. Operators should understand the best practices for operating an excavator efficiently.
Owners and operators should take these guidelines into consideration to make sure they select the proper track for the right application. With all the track options available, it doesn’t hurt to do a little bit of research before arriving on a jobsite — because one size definitely does not fit all.
Katie Pullen is Brand Marketing Manager for CASE Construction Equipment.