Buying and Maintaining a Skid Steer/Track Loader Backhoe Attachment
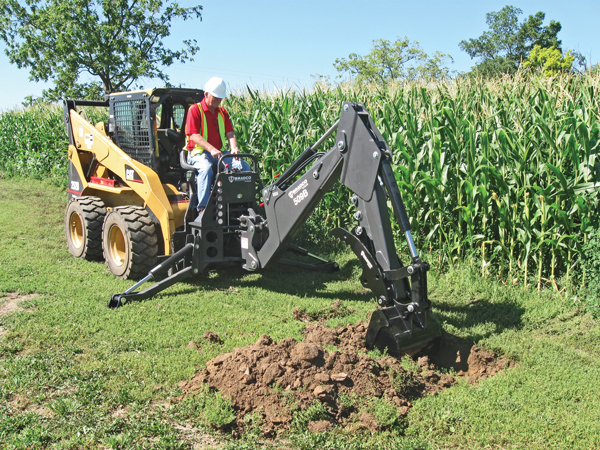
Digging a big hole doesn’t necessarily mean getting buried in big expenses — especially when dig operations are occasional and precise. Buying, owning and operating a dedicated digging machine like a mini excavator or backhoe loader will add tens of thousands of dollars to your balance sheet every year, but what about a hard-working, easily transportable, mini digger for $3,000 to $12,000 used for digging smaller projects like pipe trenches, footings, basements and drainage ditches? We suggest you consider a hydraulic-powered backhoe attachment for a skid steer or track loader, which can take your tool carrier to new levels of excavation operations.
“Due to the increasing popularity of mini excavators, we have seen a decrease in the number of backhoe attachments, but contractors who own a skid steer or track loader can very easily add a backhoe to their fleet of attachments,” says Stephen Kingsley, PLA Marketing Manager with Paladin Attachments (one of the biggest attachment makers in the United States). “It is a great addition to their toolbox for a modest investment compared to a dedicated digging machine. Depending upon the needs of the operator, a selection of buckets with varying widths are good options. Thumb assemblies and auger mounts are also practical additions that extend the versatility of this attachment.”
Backhoe attachments for skid steers and track loaders come in two main configurations today. They can be operated either inside or outside of the cab and/or incorporate the loader’s controls or have their own dedicated controls. Although boom-control backhoes (those operated with the skid steer’s levers) leave something to be desired in the way of their approximate arm reach and breakout force, the single-cylinder design to operate the bucket curl takes it easy on the hydraulic system and only requires between 11 and 22 gpm. They are also easy on the wallet, generally starting around $2,500 with an 8-in. bucket and then going up in cost depending on options.
“We have a mini backhoe, and it’s offered with or without swing,” says Ron Peters, Product Manager at Edge, the attachments brand of Manitou. “The swing option allows the equipment operator to operate the backhoe with in-cab controls to move the backhoe left and right, rather than physically moving the machine. The mini backhoe with a 12-in. bucket without swing is roughly $3,000 and a mini backhoe with swing is roughly $5,300. When it comes to operation, we recommend running the machine at the quarter throttle position to achieve a smoother operation of the backhoe.”
Taking backhoe versatility one step further, some backhoe attachments come with their own set of controls that can be used in your machine’s cab or by sitting outside the cab. Patterned in either ISO or SAE operating patterns, this style of backhoe attachment can rival the specifications of a small, dedicated compact excavator. However, the increased versatility makes more demands on your loader and wallet — costing around $12,000 to purchase.
For skid steers or track loaders with out-of-the-cab controlled backhoe attachments, the operator will need to exit the cab and saddle up onto the seat provided by the backhoe attachment. Perched atop of the attachment, the operator has excavator-style controls to manipulate the attachment, with dig depths up to around 11 ft. Vertical stabilizers and stabilizer pads, buckets ranging from 8 to 40 in. and boom attachments like thumbs can also be considered. Of course, that all depends on the manufacturer.
“We offer a variety of bucket widths with standard teeth,” explains Kingsley. “They are basic heavy-duty buckets. We do have three bucket linkage options that will position the bucket so it can open further and extend bucket reach, facilitate maximum curl or apply maximum breakout force. The boom style varies depending upon the model selected. Our largest models have standard thumb brackets to accommodate both hydraulic and fixed thumbs. We also offer quick-couplers and compatible buckets for quick bucket change capabilities.”
The beauty of the backhoe attachment is when you’re finished excavating for product installations, the attachment can be exchanged for a compactor to pack the trench, a bucket to prepare the area for reseeding or a sod roller to lay grass. A loader can even be turned into a high-performance grading machine with a laser-guided system for precision grade control. The role of a skid steer or track loader is to adapt. At widths as narrow as 36 in., these loaders can go through typical residential, commercial or municipal gates and entries where larger equipment won’t fit. On the other end of the loader spectrum, high-flow hydraulics, rated operating capacities that approach 4,000 lbs and lift arms that raise to heights of 12 ft provide the contracting industry with powerful digging and lifting capacities. A backhoe attachment is perfect for these versatile machines.
“When considering a backhoe attachment, consider safety and durability as your most important considerations,” says Kingsley. “Make sure the manufacturer stands by its backhoe and offers at least a one-year warranty. Also insist it provides detailed instructions regarding the safe use of the backhoe and make sure you familiarize yourself with the operational details before you take it on the job.”
Backhoe Attachment Maintenance
A skid steer/track loader backhoe attachment can save you money over a dedicated machine but only if you take care of it. For instance, backhoe attachments have several pivot points — swing, boom, dipper, bucket, etc. — that all need lubrication on a regular basis to ensure smooth and efficient operation. Smart folks like Peters recommend lubricating all parts provided with grease fittings daily or every eight hours, whichever comes first, with SAE multi-purpose lubricant or an equivalent SAE multi-purpose grease.
“When you fail to grease the backhoe attachment, dirt and sand are allowed to enter the pivot pins and bushings, and of course, this allows faster wear of the pins and the bushings,” explains Peters. “It’s similar to sandpaper rubbing on a surface constantly. Because it is not a minor repair to replace the pivot pins and bushings, your machine will be down for an extended period of time resulting in loss of productivity. To repair and replace the pivot pins, depending on the number of pins to be replaced, and bushings, it could cost anywhere from $500 to $1,000. To avoid costly repairs, we recommend following the recommended maintenance schedule in the owner/operator manual provided with the attachment.”
In contrast, be sure to avoid excessive greasing. Dirt collects on exposed grease and greatly increases wear, so wipe off excess grease from all fittings after greasing to reduce this wear. In fact, clean your entire machine each time you do a daily walk-around inspection, checking for problems that can be made worse if not attended to. Here are some items to look for:
- Check to see that all pins are secured with a bolt or snap.
- Inspect all cylinders to be sure there is no oil seepage around the hoses, valves or filling tube entrance.
- Make sure the hose routing is not rubbing or being pinched when the backhoe is being transported or operated and while in a folded or fully extended position.
- Look for dirt that may be caught between the stabilizer arms and cylinders, and make sure no rocks or dirt are damaging the pivot areas.
- Check the mounting system to make sure there are no loose nuts or bolts.
- Examine bucket teeth for wear and replace and tighten where necessary.
- Inspect the bucket and entire attachment to make sure there are no cracks.
Because backhoe attachments utilize a number of moving parts, checking the hydraulic oil level on your loader at least once every 40 hours of operation is crucial. It is also very important to check the oil levels when switching between attachments because different attachments may require different oil levels. AND REMEMBER: Hydraulic oil is under pressure and may be hot. Escaping hydraulic fluid under pressure can penetrate your skin, causing serious injury. Stop your skid steer or track loader engine and relieve pressure before connecting or disconnecting lines and consult your manufacturer’s backhoe operation manual for additional safety precautions before proceeding.
“The oil supply for the attachment backhoe is supplied by the loaders hydraulic system,” explains Kingsley. “When first installing the backhoe on the loader, you will need to completely extend and retract all cylinders on the backhoe several times. This will fill the cylinders with oil. Once this is done, place the backhoe in transport position, and check the oil level on the loaders hydraulic reservoir. You will most likely need to fill the reservoir to the full line. Check the oil level on a regular basis.”
Failure to maintain your loader’s hydraulic oil supply can cause serious problems with your backhoe attachment. The operation manual also commonly includes troubleshooting tips in case problems occur. Contact your local dealer or manufacturer with any questions to make sure you get the best performance possible out of your backhoe attachment.
Keith Gribbins is Associate Publisher of Utility Contractor.