Mastering Underground Pipeline Construction Techniques in Tough Conditions
By Emily Newton
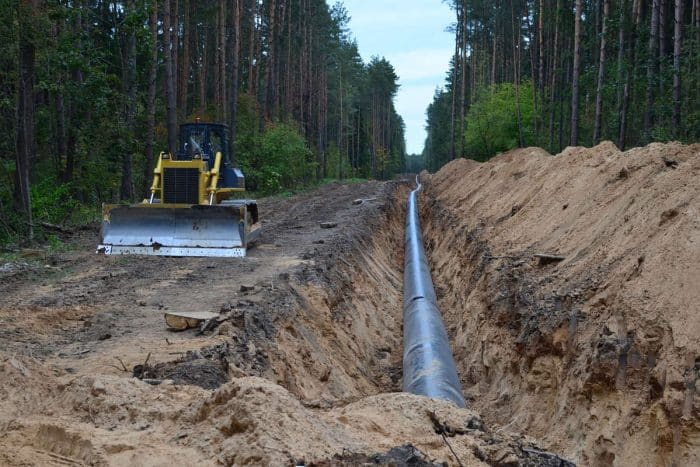
Construction is a difficult undertaking in any context. Underground pipeline construction is even more so and will likely become increasingly tough while climate issues and growing regulations add further complications. As hazards rise, teams must prepare to meet them head-on. These seven best practices can help them master their construction strategy.
Understand the Risks of Each Job
North America has over 19,000 miles of pipeline either under construction or in planning as of early 2024. While that’s great news for the industry, it heightens the need to approach these challenging projects carefully to minimize costs, delays and environmental damage.
Optimal underground pipeline construction begins with a thorough risk assessment. Experienced professionals already know the general complications to expect — regulatory hoops, unstable terrain and inclement weather, to name a few. However, it’s important to go beyond generalities and quantify the specific risk landscape of each project.
Keep a detailed record of potential issues throughout the site selection and planning phases. Work closely with the landowners, regulatory agencies and other parties involved in this process to get their insight into any specific risks. These may include unusual soil makeup, nearby utilities, seismic activity or wildlife in the area.
A site-specific, detailed risk assessment makes determining proper safety measures and workflows easier. The accuracy of a project’s design and changing specifications are two of the most common causes of delays in pipeline construction, and a more site-specific assessment addresses both.
Choose the Right Materials
Material selection is likewise crucial to uninterrupted and safe pipeline construction. While it’s easy to rely on the same, familiar resources for every project, each site and end-use presents unique considerations that deserve attention.
Sour crude — anything with a sulfur content above 0.5% — is a prime example. Hydrogen sulfide is highly corrosive, leading to stress cracking in carbon steels that might otherwise be ideal materials for their strength. Duplex stainless steels or high-nickel alloys offer more long-term resilience in these situations.
The right metal for the job should also consider the chemical makeup and physical pressures of the soil around it, not just what’s inside. Some soils are acidic and some trenches may be deep enough to warrant stronger steels to withstand the added pressure from compaction.
Base Installation Methods on Geotechnical Factors
Similarly, pipeline projects must choose installation methods carefully. Expenses and complexity are often the driving factors in these decisions, but geotechnical hazards should play a bigger role here.
Open-trench methods may be the go-to, but they’re not always the best choice. Areas with particularly wet or loose soil may require extensive tench support and dewatering with these techniques, leading to unnecessarily high spending and safety risks. Backfilling after installation may introduce further complications if a project is already running behind.
By contrast, trenchless installation can reduce risks in areas with less consistent geotechnical factors or higher environmental hazards. While this typically entails higher upfront costs from specialized equipment, it could lower expenses in the long run by preventing environmental fines, worksite accidents and schedule overruns.
Emphasize Employee Training
Masterful underground pipeline construction is also a matter of worker training. Even experienced contractors and subs can make mistakes, and human error is responsible for 90% of workplace accidents on construction sites. In light of that risk, project managers can’t overlook the importance of training and communication.
Teams must review site-specific hazards and define appropriate working behaviors before starting construction, regardless of everyone’s level of expertise. Managers should watch workers closely throughout the day to see if any common issues arise that deserve attention.
Clear workflow and chain of command guidelines can help. When everyone understands who can and can’t operate certain equipment, or who to ask about different concerns, the project will unfold with fewer injuries and errors.
Monitor Worksites
Even with thorough training, ongoing monitoring is also necessary. That’s partly because mistakes are still possible, and partly because environmental or equipment-related hazards can arise unexpectedly. Closer worksite monitoring enables faster responses to manage these changing conditions.
Technology makes a considerable difference in this area. More specifically, teams should employ Internet of Things (IoT) systems to gain real-time data on the worksite, employees and their machinery. These interconnected sensors have increased site productivity by 8.5% in some cases by enabling faster communication and improved safety.
IoT sensors can provide proximity alerts to prevent collisions, warn workers of unstable ground conditions, highlight equipment maintenance problems and more. Across all these use cases, teams benefit from real-time insight into their working conditions and hazards, unlocking new levels of safety and efficiency.
Test Pipelines After Installation
While monitoring is crucial throughout pipeline construction, ongoing reports don’t replace post-installation testing. Teams must still verify the project’s success to ensure it meets applicable standards and doesn’t require extra work.
Weld inspections are the most obvious part of this testing. Visual inspections are sometimes sufficient, but pipes with diameters above 6 inches require nondestructive testing (NDT) under federal law. Be sure that any NDT methods meet applicable regulatory standards, too. Equipment calibration is an important step in that assurance.
Testing for leaks, pressure and corrosion is similarly important. While stopping to perform this quality assurance takes time, it’s less time-consuming than managing larger maintenance issues in the future that early detection could’ve prevented.
Apply Lessons From Previous Jobs
Finally, project managers should perform an assessment after each underground pipeline installation. Compare the final time and costs to the original schedule and budget. Review any unexpected hiccups in the operation, and ask why they arose and what proved to be the solution.
These reviews may seem unnecessary at first, but they help develop more mindful project management habits. Businesses can also use these insights to inform future jobs, showing what not to do and what may work well.
Underground Pipeline Construction Requires a Unique Approach
Pipeline construction is a uniquely hazardous and complicated line of work, even compared to other infrastructure sectors. Consequently, enterprises in this industry must develop specific methods for managing these risks and complexities.
Many of these best practices boil down to adapting general concerns to project-specific considerations. Taking time in planning and construction can save time and money in the long run.
Emily Newton is a construction and industrial journalist. She is also the Editor-in-Chief for Revolutionized Magazine. Keep up with Emily by subscribing to Revolutionized’s Newsletter.