What to Consider When Renting Trench Shoring and Shielding Equipment
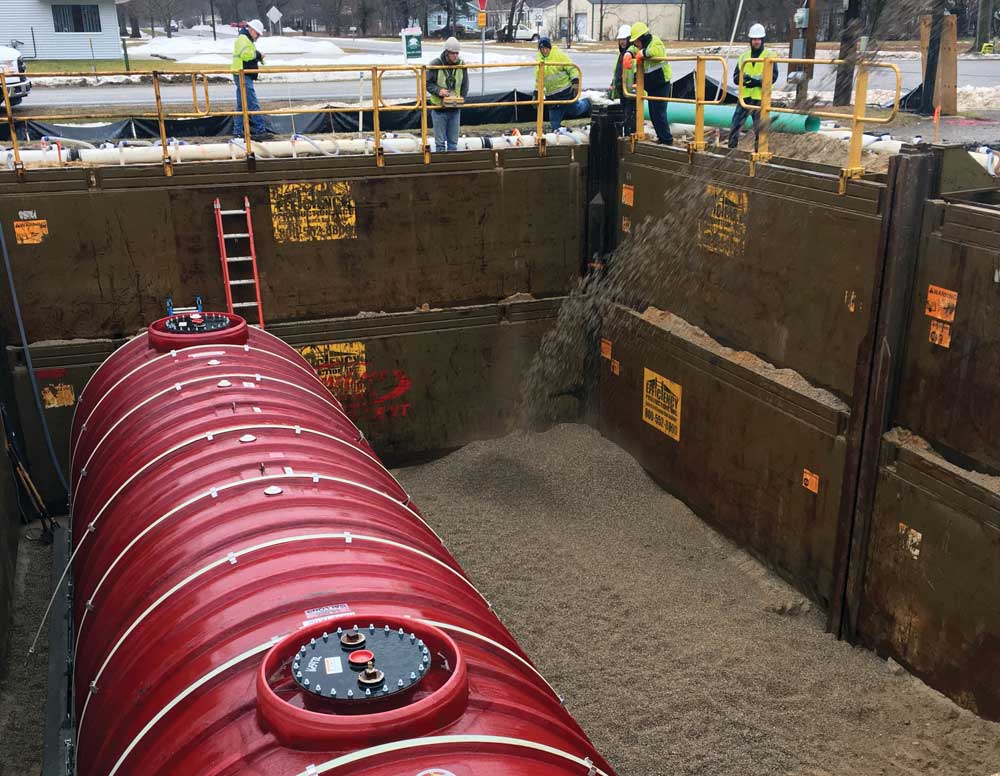
To safely shore an excavation to install two parallel storage tanks, this contractor rented a slide rail system direct from the manufacturer.
Excavation projects by definition are dangerous operations that require caution and planning, especially when the excavation is intended to create a work space for personnel such as for underground installation repair or installation. Creating a safe working area for every excavation project presents unique challenges for the contractor or municipality’s safety personnel and the work crew.
Many utility contractors own some type of trench protection device such as steel trench shields or perhaps aluminum hydraulic shores. Municipalities frequently own aluminum trench shields that can be moved with a rubber-tired backhoe. However, it is not practical or even responsible for the contractor or municipality to assume their own shoring or shielding equipment can be safely used for every excavation or site condition they encounter.
RELATED: SHELLY & SANDS Installs Deep Sewer as Part of Major Highway Project in Ohio
Excavation parameters vary greatly from project to project; including soil type, adjacent structures or buildings, and the ever-present existing underground utilities that need to be located, marked and factored into the choice of trench protection system or device. When contractors and municipalities face excavation challenges that are beyond the capabilities of their own fleet’s trench safety equipment, they must rely on rental equipment.
In today’s market, many shoring options are available through trench safety equipment rental companies or even directly from a shoring equipment manufacturer. These rental facilities and manufacturers have a well-trained sales force to assist the contractor or municipality in matching the best shoring option or solution to any specific excavation project.
This is particularly true of equipment representatives who have specialized training from the manufacturer. Experienced shoring specialists should be able to solve any excavation and safety conflict by addressing issues encountered on the job site; and it is never a one-size-fits-all solution.
A good shoring specialist will obtain as much information possible from the contractor or municipality’s designated safety official or engineering team before proposing a shoring system. The following are some important points to consider when designing a safe and appropriate shoring system for a particular excavation project.
Is this a shielding or a shoring situation?
Although commonly used synonymously, shielding and shoring are two separate protective systems with their own rules regarding proper use within OSHA standards. Shielding is a protective system utilizing a trench shield or “trench box” installed in the excavation to protect (shield) the workers from the hazards of a cave-in. Shoring is a protective system that utilizes structural members or hydraulic pressure that prevents the trench walls fro m caving in. An experienced shoring specialist can help choose the method best suited for the situation.
What is the work to be performed in the excavation and what is the proposed size and depth?
The shoring specialist has many options available from the manufacturer and the size and depth of the excavation will determine the best option to choose. Official manufacturer authorized equipment distributors offer equipment for small and shallow excavations, long pipe runs, crossing utilities, limited access and extreme depths, to name a few challenges. Rental companies with a close association with the manufacturer’s team of engineers will have access to a solution to almost any problem encountered.
What size excavation equipment is available?
When renting underground protection and production products, it is critical to factor in the size and capacity of the excavation and earth moving equipment that will be used on the project. To minimize costs to the customer, an experienced shoring specialist will match the shielding or shoring system to the heavy equipment that will be used to install the system.
The equipment distributor should be able to provide trench safety equipment that corresponds with the excavator and other heavy machines commonly used for different excavation operations. For example, a modular aluminum shielding system such as Build-A-Box™ is light enough for installation and extraction using a tractor backhoe. Comparatively, a steel trench shield 28 ft long rated for an excavation up to 30 ft deep weighs over 15,000 pounds, but well within the capacity of a typical sized track excavator that a contractor may already have in their fleet, thus eliminating the need to rent “big iron” in addition to the shoring system.
Are there any overhead utilities or other obstructions?
The proposed shoring or shielding equipment should address all concerns of the project including overhead obstructions. In most cases, options are available to utilize different rigging options to stay within OSHA standards regarding safe distances from overhead power lines. The system should be designed to provide for safe working distance from overhead hazards during assembly, installation and removal of the system.
Are there any buried utilities within excavation limits that need to be accommodated?
Dealing with utilities crossing or running parallel to the proposed excavation can cause costly delays and repairs if not addressed properly. These utilities can also create a long and frustrating day for the foreman and the contractor-designated safety person (referred to as the “competent person” on excavation projects). Some systems, such as vertical hydraulic shoring, are designed to install so crossing utilities pass through the trench with relative ease.
For larger and deeper projects with crossing utilities, a sheeting frame system such as Shore-Trak™ is an efficient and cost-effective solution. Sheeting frame systems cantilever corrugated steel sheets below a waler frame, providing better visibility during installation around existing utilities. Sheeting frames allowing efficient installation with the excavator, thus eliminating the need for a sheeting driver.
An equipment rental company or manufacturer’s shoring specialists can work out shoring solution for excavations with many existing utilities. In this case, the contractor worked with the manufacturer to design a trench shielding system that utilized lightweight aluminum sheeting to contend with the many crossing pipes and conduits.
What are the limitations of the shoring or shielding equipment?
All shoring and shielding equipment has limitations for proper use. These limitations are found in the manufacturer’s tabulated data supplied with the system. Trench shields are constructed with a maximum allowable depth of use in different soil types consistent with OSHA classifications. Hydraulic shoring tabulated data provided by the manufacturer includes a chart specifying maximum cylinder spacing for different soil conditions.
Other systems available through a rental trench store such as slide rail systems and sheeting frames will include tabulated data for the proposed configuration. Most shoring and shielding manufacturers will provide tabulated data stamped by a registered professional engineer. In some cases, a professional engineered shoring system is required and the shoring specialist should be familiar with the restrictions and requirements dictated in the tabulated data.
These items address the most common difficulties encountered on most excavation projects and should be viewed as the minimum amount of information that needs to be collected before determining the proper and safe shoring solution. In any case, the contractor or municipality should provide as much information to the shoring specialist as possible when renting trench safety equipment.
Remember, it is the mark of a well-trained shoring and shielding specialist to know the latest shoring products available, as well as the most efficient installation and removal techniques for all systems.
James McRay is Director of Marketing & Media for Efficiency Production – An Arcosa Shoring Products company. He can be reached at james.mcray@arcosa.com.
Excavation Pit Near Railroad Secured by Slide Rail System
A town near Houston needed to upgrade its storm drainage system by installing a 36-in. storm line with 48-in. casings. To complete the job, the town turned to a well-known, experienced utility Texas contractor.
The project required boring the 48-in. casings underneath an active railroad line. The bore pit had an excavation cut of 36-ft in length, 12-ft in width, and a depth of 15-ft in which the competent person onsite had originally classified the soil as Type-B. As the excavation progressed, the soil was classified for a second time as C-60. Once the excavation reached 8 ft in depth and ground water was present, the soil was classified a final time as C-80. In addition to the poor soil conditions, the site presented challenges with adjacent structures. An existing railroad line was located a few feet from the proposed bore pit. Perpendicular to the railroad was an tunnel, east of the excavation pit just a few feet away. Additionally, a live road ran north of the excavation, which contributed to the increase of pressure loads.
The nature of the excavation required a protective system that could provide enough clearance to lower the bore to its pre-determined position and have adequate space so workers could lower and feed the casings. Additionally, the contractor required a device that could support the pressure loads originated from the adjacent structures while complying with Cooper E-80 ratings. After reviewing a few protective systems, the contractor selected a slide rail system from NTS with rolling struts and a sheeting guide frame. The slide rail system is a modular protective system that can be paired with numerous applications.
For this project, steel sheets and the sheeting guide frame were added to minimize soil disturbance and provide support along the depth of the excavation where the bore be feeding the 10-ft casings. In addition, the rolling struts provided the ability to add additional support while allowing the contractor to adjust its placement for vertical clearance. The contractor was extremely satisfied with the modular capabilities of the slide rail and how well it paired with the sheeting guide frame and the rolling struts which added additional support and reduced the soil disturbance.
Source: NTS
RELATED: NTS Expands To United Kingdom Tags: May June 2019 Print Issue