How to Find the Right Fit for Your Auger Boring Project
A horizontal auger boring contractor working underground from Point A to Point B can encounter some interesting things. One crew bored into buried farm implements that presumably had been dumped in a ditch and covered with soil. “Horizontal boring is not a business for the faint of heart,” says Jim Weist, president and owner of Michael Byrne Mfg. “You can run into things totally unexpected, from large boulders to different striations of material to abandoned fuel tanks.”
His point is that the boring machines drilling through the earth must be built to withstand the shock of plowing into… well, a rusty plow. “At Byrne, we make our own gear box, the heart of the boring machine, and we make it so it can withstand shock,” Weist says. “It is just a heavier-duty rig, that’s what our customers tell us. Built like a tank.”
Toughness indeed is one criteria for utility contractors who are evaluating a horizontal boring machine but not the only one. Contractors need different machines with different capacities and capabilities. One size does not fit all. Most utility auger bores — as opposed to cross-country pipelaying — range from 12 to 36 in. in diameter, primarily for water or sewer systems, but also to contain lines. That being said, Weist just returned from a job where multiple 72-in.-diameter tunnels were being drilled under a Phoenix interstate.
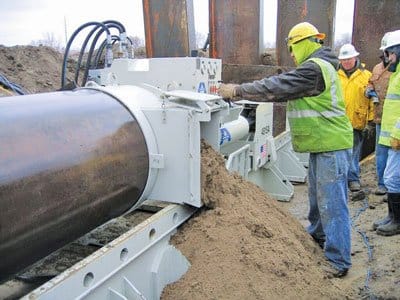
Most utility auger bores — as opposed to cross-country pipelaying — range from 12 to 36 in. in diameter, primarily for water or sewer systems, but also to contain lines.
The length of a bore is another factor. A 12- to 36-in. bore typically runs from 120 to 220 ft, whereas a bore 5 or 6 ft in diameter may run 350 ft or longer, with some extending up to 900 ft. This is significant because the larger the casing and the longer the bore, the more powerful the boring rig to bore it.
Soil conditions have a lot to do with how much torque and thrust is needed. If the ground is sugary sand or sticky clay, thrust is vital because that type of soil sucks in around the casing, binding it with friction. A machine must be able to thrust through it. “But with stiffer clay or light rock, torque is what you run out of before you run out of push,” Weist says. That is, a rotating drill head must be able to keep cutting through a tough material despite the resistance.
The reason for a bore also determines the machine. Bores of 6 in. in diameter or less are usually for fiber-optic or electric lines and small water pipes. They are suitable tasks for surface-launched horizontal directional drill (HDD) rigs. But some water and all gravity sewer lines must begin and end on grade, which requires that an auger bore rig be set up on grade at the bottom of one excavated pit and run to a second pit.
Where extreme accuracy is required, guided boring machine (GBM) systems are used with an auger boring rig. The GBM system installs pilot tubes and the lead tube contains a steering head for soil displacement and houses a LED target. The rig operator monitors the location of the target from the monitor on the jacking frame, visible through the interior channel in the pilot tubes string, and makes line and grade steering corrections. The GBM system is then removed and the casing and augers follow the pilot tube bore path. “The whole thing about guided boring is accuracy,” says Terry Fisher, product manager at Akkerman Inc.“ We pride ourselves in knowing that our equipment makes it possible for contractors to being able to hit the other side several hundred feet away within a quarter of an inch.”
Such accuracy frankly is astounding. It lets a project owner select a precisely-sized steel casing instead of oversizing to compensate for divergence from a path, Fisher says. He adds that the underground clutter of lines and pipes increasingly requires such accuracy. “The easement windows are getting narrower and narrower.”
On the other hand, all those utility lines will need replacing eventually, which bodes well for the future of the auger boring industry. “Honestly, with so much infrastructure beneath ground level, a lot of rehab work will be going on,” says Justin Watson, northeast regional salesman for McLaughlin. “We expect that to grow over the next 10 to 20 years.”
McLaughlin’s most popular rig for utility work is the MCL 24B, which is ideal for case boring projects from 4 to 24 in. in diameter. The rig’s air-cooled high-torque 31-hp Deutz diesel engine produces 115,000 lbs of thrust and 8,500 ft-lbs of thrust. Most boring today, incidentally, is inside a casing. Free boring still occurs in jobs up to 8 in. in diameter, but larger diameter free boring generally is avoided.
“A case bore is just a lot safer,” Watson says. “In the last 20 years, people got away from free boring because of risk of injury.” The safety comes from not exposing workers to the rotating auger. Furthermore, if a bit hits rock or some other obstruction, a resulting deflection will not be transmitted dangerously to people back in the pit.
To accommodate different job opportunities, many utility contractors have several auger bore rigs in a fleet. For a small diameter bore of up to 10 in. in congested urban settings, a contractor might use a McLaughlin 12HB Zipper, which can operate from a trench just 7-ft long and be powered by hydraulic lines running down from a backhoe or mini excavator.
A contractor with bigger designs might have a 48-in. rig, as well as a larger Michael Byrne D60/72-1.5M rig with a 250-hp diesel engine that produces 1.5 million lbs of thrust and 220,000 ft-lbs of torque. Small contractors don’t have such machines simply because they are too big. “The total machine can weigh over 50,000 lbs,” Weist says. “You have to be a contractor with the capacity to move and handle such a rig.”
Auger boring technology is evolving to battle rocky soils. Akkerman offers a new product that allows guided pilot tubes to cut through soft rock of up to 12,000-psi density. A new Akkerman rock boring unit in the GBM 4800 Series can install 36-in. steel casing through rock up to 18,000 psi.
McLaughlin continues to emphasize safety. It places its operator platform on the right side of the machine to reduce danger in case an auger seizes up and starts to roll over. For the same reason, McLaughlin’s patented Operator Presence Control clutch allows instant disengagement of the engine from the auger drive. Also, this month the manufacturer is bringing out a new 60-in. bore rig with a Tier 4 Final engine.
Michael Byrne Mfg. has been manufacturing bore rigs for 51 years — the 93-year-old company namesake still keeps an eye on the firm, Weist reports — and this year will introduce Tier 4 models. It also offers a new swivel cutting head that fits on guided bore pilot tubes to take some of the bore rig’s thrust. The company recently fabricated two specialty machines for remote control burial of nuclear waste and Weist sees the remote technology being adapted to further reduce bore pit dangers.
Auger boring took a hit when HDD first came on the market, but that market loss has been arrested. Because directional drilling tends to create more voids, for example, auger bores are now preferred under railroad beds. Fisher says conversations with Akkerman customers indicate the industry is emerging from the post-recession slump. “Most of the contractors we work with have expanded their crews. They say they are the busiest they have ever been.”
Giles Lambertson is a freelance writer for Utility Contractor.
Click here for more articles on auger boring. Tags: Akkerman, Auger Boring, March 2017 Print Issue, Mclaughlin, Michael Byrne Mfg.