Experts Sound Off on the Latest Innovations in HDD
A quarter century ago, when horizontal directional drilling (HDD) entered the underground utilities market, the ground was less crowded. Lines and pipes were fewer and had been laid for the most part on the bottoms of open trenches of predictable depth. Today, the subterranean landscape is much different.
Drilling contractors now burrow into soils cluttered at varying levels with natural gas and water pipes, power lines and fiber-optic cables. The good news is that underground tracking technology has kept pace with this proliferating demand — and equipment manufacturers are producing drilling rigs to match.
“We have better tools today to produce a successful project, from designing the project to executing it,” says Tod Michael, Trenchless Product Manager at Vermeer. He has seen these tools evolve during two decades at the manufacturer. “We have a better understanding of what a successful bore looks like from a design standpoint. We have better drilling fluid products. The electronics have definitely changed, the locating electronics to track the drill head. We have all of that as an advantage that we didn’t have 25 years ago.”
And contractors today have some better choices in HDD rigs. Most of the operating rigs in this country are small — under 40,000 lbs of pullback force, according to a 2015 market survey of HDD owners. The biggest share of the working market is boring tunnels for versatile, high-density polyethylene pipe.
In this class of horizontal drills, Ditch Witch promotes its JT25 model as a unit designed specifically for utility contractors. The machine produces 4,000 ft-lbs of torque and 27,000 lbs of thrust and pullback. The unit was introduced three years ago, but now is powered by a 130-hp Tier 4 Cummins diesel engine and offers telematics connections and a wireless ground control unit.
“We pushed the envelope when the JT25 was developed, stressing speed, power, productivity and overall reliability,” says Seth Matthesen, Senior Product Manager and 27-year veteran of the HDD industry. Ditch Witch customers also can opt for the JT30 — or the JT30 All Terrain — when a job requires more backreaming or punching through rock. These two 160-hp drills have performance characteristics comparable to the JT25, and the All Terrain unit’s drill bit is mechanically turned, therefore requiring minimal amounts of drilling fluid.
Over at Vermeer, a 100-hp Deutz Tier 4 Final engine on the D23x30 S3 drill produces 24,000 lbs of thrust-pullback force and 3,000 ft-lbs of torque. “That particular machine really puts out a lot more power in a small footprint than what has been done in the past,” says Michael. “It really matches up well with urban utility work. It’s compact, but also is a machine that has a significant amount of data for machine health and operation.”
Vermeer utility drills include its D24x40 S3. It has a 125-hp John Deere power unit that produces thrust-pullback force of 28,000 lbs and 4,200 ft-lbs of torque.
In the Toro lineup is the DD2024, a popular directional drill for utility projects. Its Cummins diesel is rated at just 74 hp and produces 2,400 ft-lbs of torque and 20,000 lbs of thrust and pullback force. “We think we have optimized the machine performance and hydraulics, coupled with a very small package that sets it apart in the marketplace,” says Josh Beddow, Marketing Manager for Toro’s sitework systems. If more power is needed, model DD4050 is powered by a 160-hp Cummins engine that turns out 5,000 ft-lbs of torque and a full 40,000 lbs of thrust and pullback.
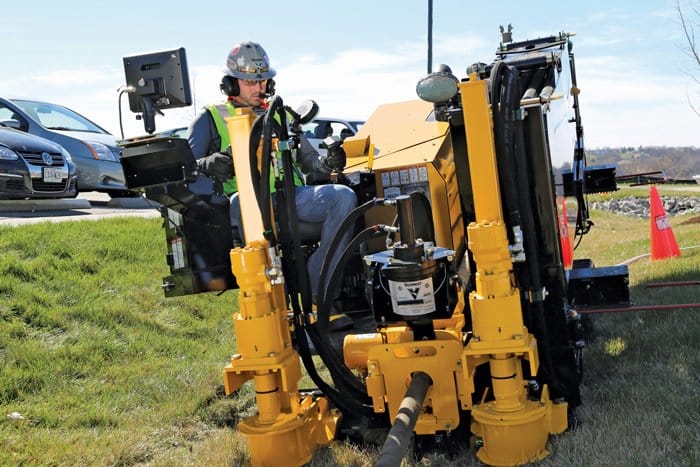
In an effort to retain and attract a capable HDD workforce, Vermeer recently began to offer an intense two-week training program for contractor employees called HDD Circuit — mixing classroom time with hands-on experience.
A directional drill usually is evaluated in terms of its torque at the head end of the drill string and its thrust force, as well as drill rotation speed and mudflow during pullback. “All of these drill components work in combination,” says Matthesen. “Not every job is going to utilize all of them, but when you do get into a position that you need all of them simultaneously, you can confidently do the job.”
But other features attract buyers, too. Vermeer emphasizes how its drills can be configured for optimum performance. “What we do today is make our machines so a customer can configure a machine to fit an application,” says Michael. “We allow a lot more setup variations so you can optimize a machine’s capability. Some of our competitors are following us down this path.”
Toro stresses its “smart” electronics, such as its auto-throttle control that senses lack of input during a boring when an operator is either inattentive or distracted. At that point, the engine idles down — but ramps up to the previous rpm when an operator returns to the joystick. The feature ensures the unit is being operated safely and for maximum production.
Ditch Witch manufactures its own directional drill pipe, a step it took to better match pipe to drill. “As the innovator of HDD, we looked at several drill pipe options but they never perfectly fit our horizontal method, so we decided to design our own,” Matthesen says. Pipes are designed individually for each machine’s torque and drilling application — only the JT25 and JT30 have interchangeable pipe. Three years ago, Ditch Witch started offering pipe that fits competitors’ drills so customers with mixed equipment fleets can one-stop shop.
All of these directional drills are easily capable of boring 400 to 500 ft, far enough to run a cable or pipe beneath a residential or commercial block, pass under a street or dive under a stream. Their pilot bores typically are 2 to 6 in. in diameter and, for short distances, they can pull back a reamer of up to 30 in. While some of these units can bore a 1,000 ft, pullback capability over such lengths is limited.
Operator displays and diagnostics vary somewhat, some being more customizable than others, but all monitor what’s happening out of sight at the end of the string. In respect to joystick controls, some manufacturers use one, others two and some offer the option of each. “We run two joysticks,” says Michael. “It is a little bit about operator preference. What we find is that if an operator learned on a dual joystick machine, he prefers to operate a dual joystick machine.”
The increased sophistication of these HDD units comes as the construction industry struggles to retain and attract a capable workforce. In response, directional drill manufacturers are upping training opportunities.
In December, Vermeer began to offer an intense two-week training program for contractor employees called HDD Circuit. It mixes classroom time with hands-on experience. In the first quarter of this year, Ditch Witch will introduce a comprehensive training program with online and classroom courses, an HDD simulator and onsite training for contractors and equipment operators. Toro regularly offers training through its dealer network, both for new customers and old ones who are learning new technologies and upgrading their diagnostic skills.
So the underground utilities industry continues to benefit from evolving technology. Like an out-of-sight bore head, it confidently thrusts ahead. Toro, for example, promises a new operating system in the spring that, Beddow says, “really is a step up from our previous system. It is so intuitive and is an overall much easier system.”
Engineering breakthroughs are about to come more quickly now that the EPA’s diesel engine mandates have, for the time being, run their course. Matthesen says the engine tier requirements precluded some industry-wide spending on other innovations. “It would be nice, at some point, to get to where we can have a five- or 10-year run without mandated engine modifications.”
Giles Lambertson is a Freelance Writer for Utility Contractor. Tags: Ditch Witch, March 2016 Print Issue, Toro, Vermeer