The Groundbreaking Success of Pipe Jacking and Microtunneling in Construction
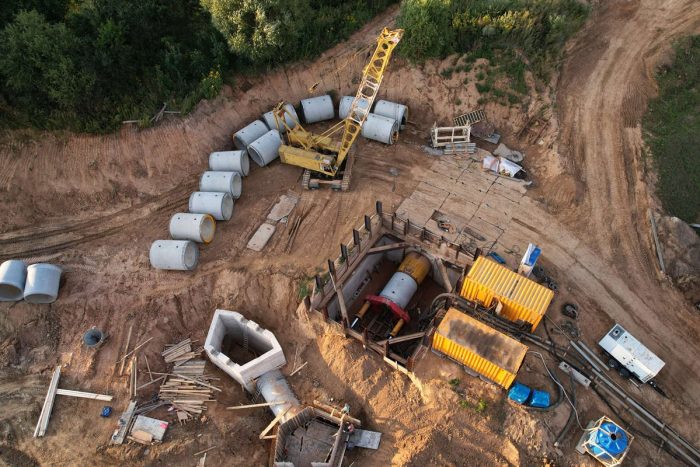
By Emily Newton
Pipe jacking and microtunneling have emerged as more effective approaches than traditional open-cut excavation. While project managers often compare the practicality of jacking vs. microtunneling for specific use cases, both can be more precise, cost-effective and efficient than their counterparts. How do they lead to success?
The Alternatives to Open-Cut Excavation
Open-cut excavation is time-consuming, expensive and disruptive. Trenchless methods like pipe jacking and microtunneling are groundbreaking alternatives that offer more flexibility, accelerated project completion rates and less surface disruption.
Pipe jacking involves a hydraulic jack that uses thrust power to push a prefabricated pipe into the borehole while simultaneously excavating the ground. As the soil exits the jacket pipe, workers must be present to remove it using wheeled carts or vacuum extraction systems. It is ideal for GRP, steel or clay pipes ranging from 150 millimeters to 2,400 millimeters in diameter.
In contrast, microtunneling — a form of pipe jacking installation — is a remotely controlled method involving a laser-guided microtunnel boring machine (MTBM). An operator must be present at all times to gauge the progress and control the machine as bores through the ground to create a tunnel for pipes to be laid.
In the past, microtunneling exclusively referred to smaller-diameter pipe jacking techniques. Now, it relates broadly to larger-diameter pipeline installations remotely controlled by above-ground operators.
While open-cut excavation equipment is generally more common, its trenchless counterparts often outperform it. However, both types have unique weaknesses. Project managers must assess the practicality of jacking vs. microtunneling to determine which is best for their project.
Trenchless Pipe Jacking vs. Microtunneling
When comparing pipe jacking vs. microtunneling, decision-makers must consider their project requirements, budget constraints and soil conditions.
Trenchless Pipe Jacking
Trenchless pipe jacking is ideal for time-sensitive construction projects requiring larger pipe diameters. It is faster and more cost-effective than microtunneling because it relies on less complicated equipment. For instance, instead of using a laser-guided MTBM, it utilizes a thrust guidance system. Notably, it is limited to straight-line installations.
Microtunneling
Microtunneling is ideal for construction projects under existing infrastructure or ground obstacles because its laser-guided system and smaller pipeline diameter enable high precision. Unlike trenchless pipe jacking, it is suitable for rocky terrain.
Although microtunneling is more precise than pipe jacking, it is more expensive, requires a more extensive setup process and takes longer to complete. For these reasons, it is often only used for logistically complex projects.
The Role of Pipe Jacking Techniques in Microtunneling
While trenchless methods are more time and cost-effective than their open-cut counterparts, they face the issue of misalignment. Properly aligning the launching and reception pits for underground construction projects can be challenging since excavation happens out of sight. Crews must rely on their equipment to ensure trajectory and orientation remain accurate.
While a variety of guidance, monitoring and correction technologies exist to mitigate pipe misalignment, unforeseen circumstances like soil shearing or pipe damage can cause it to happen regardless of preparation. Considering it can impact the structural integrity of the entire project, maintaining alignment is vital for trenchless construction.
Although microtunneling has more selective use cases than trenchless pipe jacking, it is less likely to cause soil shearing because it is minimally invasive. Additionally, it allows for greater flexibility because it can handle small-diameter pipes and curved routes.
Depending on a project’s requirements, it may involve pipe jacking and microtunneling. Soil conditions, budget constraints, route complexity and ground obstacles are some of the main deciding factors project managers and engineers should consider when determining whether or not to use pipe jacking techniques in the microtunneling process.
How Pipe Jacking and Microtunneling Maintain Alignment
For more complex projects, a combination of jacking and microtunneling may be ideal since pipe-jacking techniques help construction crews maintain pipe alignments throughout the microtunneling process.
Setup
The angle of the launching and reception pits where the construction crew initially set up the jacking equipment and pipes is critical in ensuring proper pipe alignment during the microtunneling process.
In the case of one residential development project, three shafts — each with diameters of 6,500 millimeters — were set up 8-12 meters deep for the launching and reception pits for two pipe jacks. The crew used pipe jacking techniques strategically to prevent disruption to nearby domestic properties while completing the wastewater sewerage network.
Progress
Pipe jacking machines are essential for maintaining alignment during microtunneling. For instance, the guided thrust system ensures consistent, steady progress, controlling alignment as excavation progresses. Notably, MTBMs are smaller than typical tunnel boring machines, enabling operators to control the direction of pipes with greater precision.
Monitoring
Pipe jacking equipment often includes guidance systems to provide feedback on the pipeline’s location and orientation as excavation progresses. This way, operators can detect angle discrepancies, ground obstacles or course divergences to prevent misalignment proactively.
Guidance systems like gyro units and lasers help operators ensure the pipeline follows its intended path. If they notice a deviation, they can respond in real time to correct it and prevent it from happening again. In this way, pipe jacking techniques help them maintain their project schedule and ensure the integrity of their final structure.
Correction
Operators can make adjustments to their pipe jacking equipment to maintain trajectory despite unexpected ground obstacles or angle discrepancies. For instance, they can leverage variable speed control to accommodate changing soil conditions. These minor modifications ensure alignment through the microtunneling process.
In the case of China’s first ultra-long-distance pipe jacking project — a 16.2-kilometer route — the operators leveraged variable thrust force and a retractable pipe jacking machine to navigate the complex mix of limestone, fractured rock and mudstone while preventing pipe misalignment.
The Bottom Line of Pipe Jacking and Microtunneling
Compared to open-cut excavation methods, construction companies utilizing pipe jacking and microtunneling will achieve precision and cost savings regardless of application. It is in their best interest to determine which is best for their project — or if a combination is ideal — to maximize their revenue and achieve optimal completion rate acceleration.
Emily Newton is a construction and industrial journalist. She is also the Editor-in-Chief for Revolutionized Magazine. Keep up with Emily by subscribing to Revolutionized’s Newsletter.